Полеты станут безопаснее и дешевле, благодаря снижению массы авиационного насоса на 17%
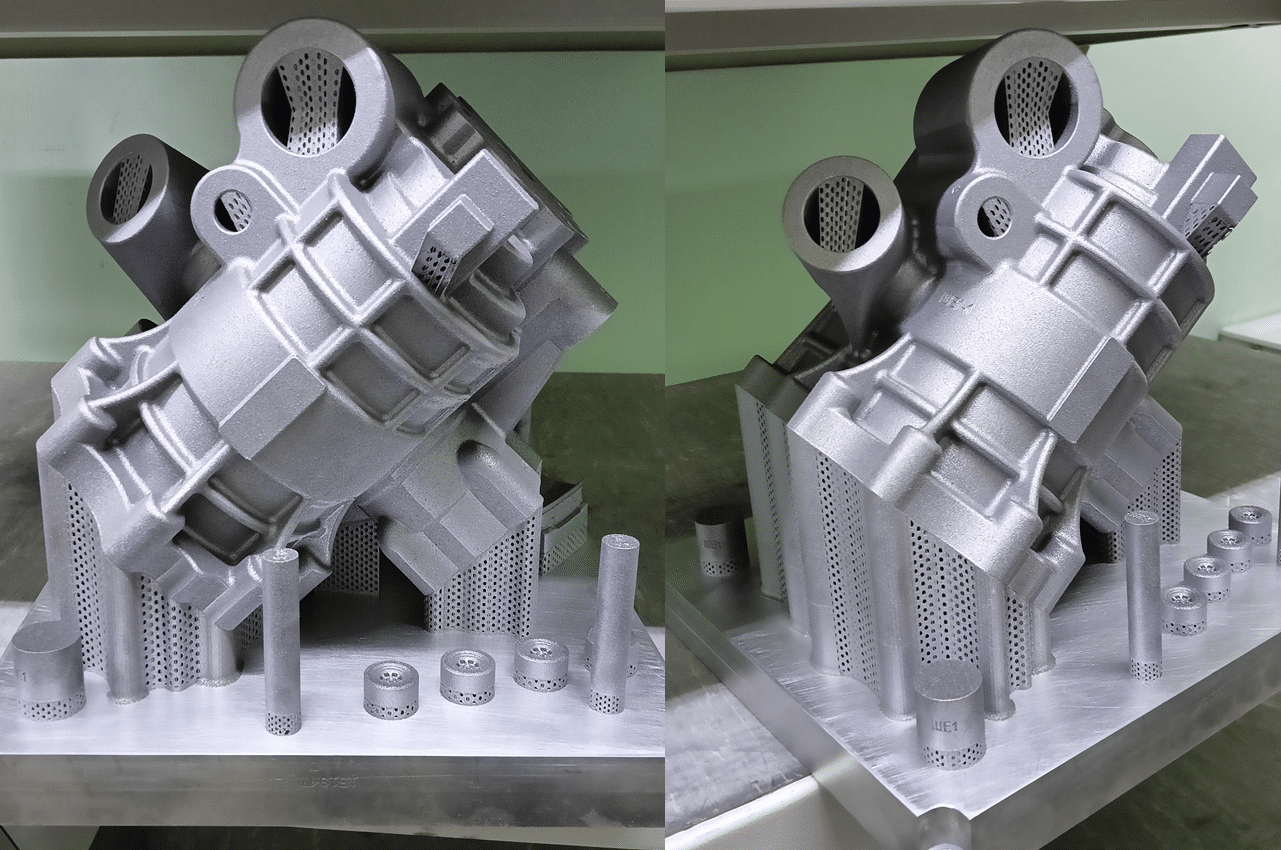
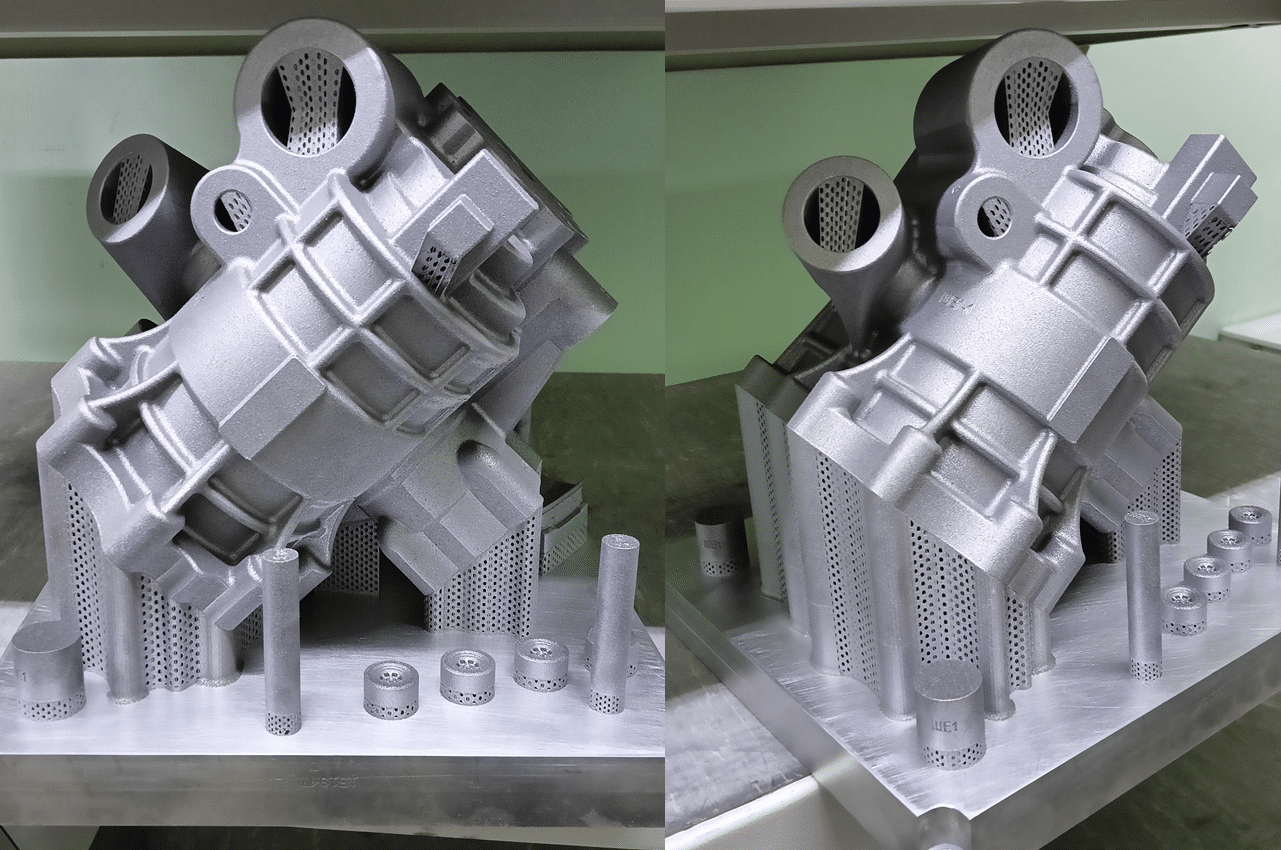
Корпус насоса на подложке / © Виталий Вишняков, пресс-служба ПНИПУ
Полеты станут безопаснее и дешевле, благодаря снижению массы авиационного насоса на 17%
Статья опубликована в сборнике материалов конференции «Химия. Экология. Урбанистика». Исследование проведено в рамках программы стратегического академического лидерства «Приоритет-2030».
Гидравлический насос создает движение жидкости по трубам или каналам, что приводит в действие другие устройства — например, гидроцилиндры или гидромоторы. Особенно жесткие требования предъявляются к авиационным шестеренным насосам – одному из видов таких гидравлических систем. Они отвечают за подачу топлива к двигателю, и от их надежности и эффективности зависит безопасность всего воздушного судна. При этом эксплуатируются они в экстремальных условиях повышенных температур и давления.
Поэтому современные требования к шестеренным насосам очень высоки. Они должны быть не только надежными и долговечными, но и легкими и компактными, что критично для летательных судов, которые вынуждены поднимать в воздух сотни тонн. Меньший вес позволяет расходовать меньше топлива, снизить напряжения и износ деталей, увеличить их срок службы – все это повышает безопасность полетов.
Большинство изделий сегодня делают по традиционным технологиям (фрезерование, литье, сверление), что приводит к громоздкой конструкции с множеством деталей, избыточным весом и габаритами. Само производство долгое, сложное и требует больших затрат, так как для изготовления точных корпусов необходима длительная техническая подготовка. Набирает популярность изготовление с помощью 3D-печати, однако возникает другая проблема: принтер «выращивает» деталь слой за слоем, начиная снизу, и получается так, что некоторые отвесные детали не имеют под собой опоры – в этом случае для того, чтобы их возможно было напечатать, нужны поддерживающие структуры – металлические опоры. После печати их нужно удалять, но это увеличивает трудоемкость работы, а на месте удаления остаются следы, которые могут ухудшить качество поверхности и привести к браку.
Эти проблемы решили ученые Пермского Политеха. Они модернизировали конструкцию авиационного шестеренного насоса и технологию его изготовления, что позволило снизить массу корпуса на 38,5%, а также сократить количество операций, необходимых для производства, с 40 до 31, время механической обработки – с 4 000 до 1 100 минут, а термической – с 1 800 до 400. Исследование провели на примере конкретной модели, но эти методы можно применить и к другим гидравлическим агрегатам.
– Исходным объектом стал корпус шестеренного насоса массой шесть килограммов из алюминиевого сплава АК4-1. Этот материал широко применяется в ракетно-космической и авиационной промышленности, в том числе в пассажирском Ту-204/214. Его конструкция имела существенные недостатки: излишне толстые стенки, большое количество сверлений для внутренних каналов, необходимость в установке заглушек, высокая трудоемкость сборки и, как следствие, высокая стоимость производства. Эти факторы увеличивали вес, габариты и цену агрегата, а также снижали его надежность, – комментирует Евгений Гашев, заведующий учебной лабораторией, доцент кафедры «Инновационные технологии машиностроения» ПНИПУ, кандидат технических наук.
В процессе изготовления исследователи использовали технологию аддитивной печати, причем конструкцию спроектировали с минимальным количеством поддерживающих металлических опор, что снизило трудоемкость постобработки и риск брака. Материал заменили аналогом – алюминиевым сплавом AlSi10Mg, который обладает лучшими прочностными характеристиками по сравнению с традиционным.
– В новой конструкции насоса мы отказались от клапана постоянного давления за счет перспективной конструкции клапана предохранительного, в котором высокое давление внутри обеспечивается без дополнительного узла. Также мы переместили клапан, фильтр и магнитная ловушка, которая «ловит» вредные металлические частицы в потоке, – они установлены на выходе топлива. Это улучшило очистку рабочей жидкости и лучше распределило вес. Вместо громоздкого внешнего канала для перепуска топлива сделали компактный внутренний, а для сохранения прочности добавили пояс и ребра, – рассказывает Виталий Вишняков, магистрант Передовой инженерной школы «Высшая школа авиационного двигателестроения» ПНИПУ.
Все эти модификации снизили массу корпуса до 3,7 килограммов, то есть на 38,5%, а всего насоса — на 17%. При этом сохранена достаточная прочность корпусе, что гарантирует надежность даже в экстремальных условиях высоких температур, давления и вибраций, которые испытывают на себе двигатель и его элементы во время полета. Прочностной анализ подтвердил, что максимальные напряжения (247 МПа) и деформации (0,93%) находятся в допустимых пределах.
Разработанная конструкция уже успешно прошла испытания, сейчас ведется подготовка к серийному производству. Планируется модернизация подшипников и подпятников шестерен, что позволит еще больше снизить массу насоса. Источник материала и фото: "Naked Science"